The Art and Craft of Ceramic
Ceramic refers to any object made from natural materials like clay, earthen minerals, and water, which are then hardened by heating them to high temperatures.
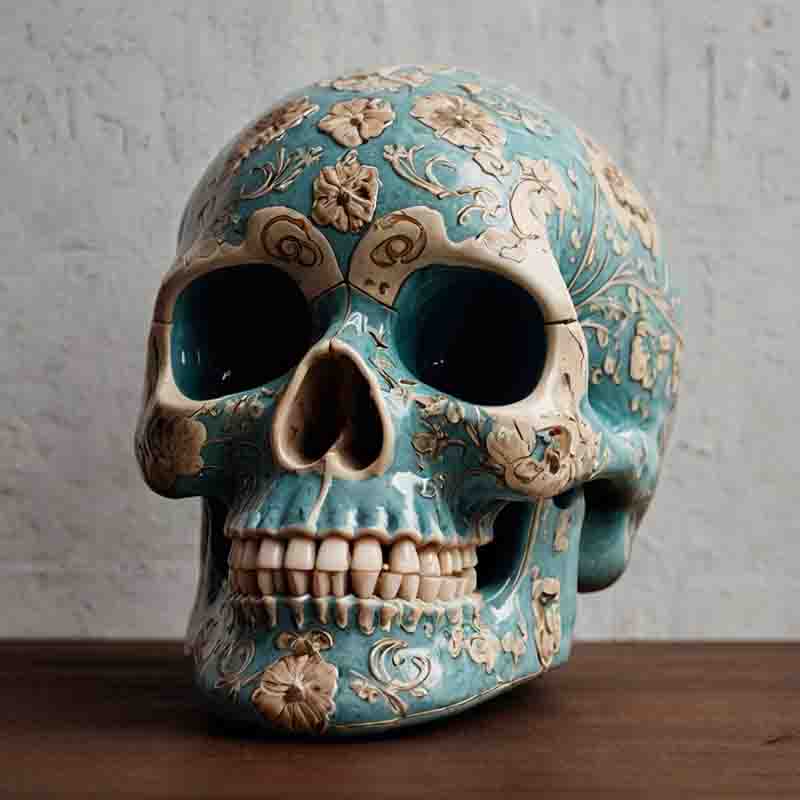
Archaeological ceramics help researchers study past societies through pottery styles, firing methods, and decorations.
Ceramic refers to a wide range of items created from inorganic, non-metallic materials like clay, silica, and feldspar, shaped and hardened through heat.
Its use spans thousands of years, encompassing artistic, functional, and industrial purposes.
The foundation of ceramics lies in clay mixed with water, combined with other materials like kaolin, feldspar, and silica to enhance its properties.
Additives like sand or grog improve strength and workability.
Other advanced ceramics involve materials such as oxides, carbides, and nitrides, used in high-tech applications.
Different types of clay include:
-
Porcelain: Known for its strength and translucence, used in fine china and decorative items.
-
Stoneware: Durable and high-fired, ideal for functional pottery.
-
Earthenware: Low-fired and porous, commonly used in terracotta and decorative pottery.
These materials vary in composition and firing temperature, influencing the final product’s texture, strength, and finish.
Ceramics have been integral to human history. Ancient civilizations like the Egyptians, Chinese, and Greeks used ceramics for both utility and art.
These artifacts provide insights into technological advancements and cultural practices of their time.
Common Types of Ceramics
Type | Temperature Range | Characteristics | Common Uses |
---|---|---|---|
Earthenware | 900–1,150°C | Porous, Soft | Pottery, Bricks |
Stoneware | 1,100–1,200°C | Dense, Durable | Dinnerware, Bakeware |
Porcelain | 1,200–1,400°C | Fine, Smooth, Translucent | Fine china, Tiles |
Advanced | Varies by material | Strong, Heat-Resistant, Specialized | Electronics, Aerospace |
By understanding the different types, applications, and maintenance of ceramics, we gain a deeper appreciation for their value in both history and modern society.
Ceramics play a critical role in both creative and industrial fields. Their versatility, durability, and aesthetic potential make them a key material in human innovation and expression.
12 Facts To Know About Ceramic
-
Definition: Ceramics are non-metallic, inorganic materials shaped and hardened through heat, making them durable and versatile for artistic, functional, and industrial use.
-
Ancient Cultures: Ceramic art has played a central role in many ancient cultures, including the Greeks, Romans, Chinese, and Middle Eastern societies.
-
Types of Clay: Porcelain (Strong, translucent, and high-fired), Stoneware (Durable, dense, and suitable for functional items), Earthenware (Porous, low-fired, and commonly used for decorative pieces).
-
Production Techniques: Hand-Building (Shaping clay manually), Wheel-Throwing (Using a potter’s wheel for symmetrical forms), Slip-Casting (Pouring liquid clay into molds for detailed designs).
-
Firing Process: Firing in a kiln solidifies clay and glaze, with temperatures ranging from 1,000°C for earthenware to over 1,400°C for porcelain.
-
Glazing: Glazes add color, texture, and a protective coating to ceramics. They consist of minerals and oxides that melt during firing to create a glass-like surface.
-
Artistic Value: Ceramics are used in sculptures, pottery, and decorative tiles, offering endless opportunities for creative expression.
-
Industrial Applications: Ceramics play a vital role in industries like electronics, aerospace, and medicine due to their heat resistance, strength, and insulating properties.
-
Cultural Importance: Historical ceramics, from ancient Greek amphoras to Chinese porcelain, provide insights into past cultures and technologies.
-
Common Issues in Production: Problems like cracking, warping, or glaze defects can occur. These are often resolved by refining drying methods, firing conditions, or material formulations.
-
Conservation and Restoration: Ceramic artifacts are preserved using archival adhesives and cleaning methods to repair damage and maintain their historical integrity.
-
Modern Advances: Innovations in advanced ceramics include applications in high-tech industries, such as ceramic coatings for aerospace and bio-ceramics for medical implants.
This concise list covers essential knowledge about ceramics, from their origins and processes to their applications and significance.
Ceramic: Timeline
Ceramics have been an essential part of human history, dating back to around 10,000 BCE.
Early civilizations used clay to craft tools, vessels, and art, shaping materials by hand before the invention of the potter's wheel.
The medium keeps flourishing, combining ancient methods with modern advances and serving both useful and artistic purposes worldwide.
Year | Milestone |
---|---|
10,000 BCE | The earliest known ceramics, such as the Venus of Dolní Věstonice figurines, are created during the Upper Paleolithic era. |
9,000–8,000 BCE | Pottery emerges in East Asia (China, Japan, Korea) with the creation of utilitarian vessels for cooking and storage. |
7,000 BCE | Ceramics spread to the Middle East, with early examples found in Mesopotamia and the Levant. |
6,000 BCE | The first evidence of glazed ceramics appears in Egypt, used to create decorative tiles and ornaments. |
5,000 BCE | The invention of the potter’s wheel in Mesopotamia revolutionizes ceramic production, allowing for more uniform vessels. |
4,000 BCE | Painted ceramics emerge in Persia and the Indus Valley, showcasing artistic patterns and designs. |
3,000 BCE | Chinese Longshan culture produces black pottery, highly valued for its thin walls and glossy finish. |
2,000 BCE | The Bronze Age sees ceramics used for both practical and ceremonial purposes across Europe, Asia, and the Middle East. |
1,500 BCE | Mycenaean and Minoan civilizations create sophisticated pottery with marine and floral motifs. |
1,000 BCE | The Etruscans and Greeks refine ceramic art, producing black-figure and red-figure pottery with mythological themes. |
500 BCE | Terra sigillata, a type of fine, glossy Roman pottery, becomes popular throughout the Roman Empire. |
1st Century CE | Porcelain is invented in China during the Han Dynasty, known for its strength and translucency. |
9th Century CE | Islamic cultures advance ceramic techniques, introducing tin-glazing and intricate geometric patterns. |
11th Century CE | Chinese Song Dynasty potters perfect celadon glazes, producing iconic jade-green finishes. |
13th Century CE | Maiolica, a type of tin-glazed pottery, becomes popular in Italy, showcasing vibrant Renaissance designs. |
16th Century CE | European potters begin replicating Chinese porcelain after its introduction via the Silk Road. |
18th Century CE | Josiah Wedgwood revolutionizes ceramics in England, producing refined earthenware for the middle class. |
19th Century CE | Industrialization allows for mass production of ceramics, reducing costs and expanding accessibility. |
20th Century CE | Studio pottery movements emphasize hand-crafted ceramics as art, led by artists like Bernard Leach and Lucie Rie. |
21st Century CE | Contemporary ceramics blend traditional techniques with modern technology, such as 3D printing and digital design tools. |
This timeline reflects ceramics' evolution from utilitarian tools to fine art and industrial products, illustrating its cultural and technological significance through the ages.
Exploring the Diverse World of Ceramic
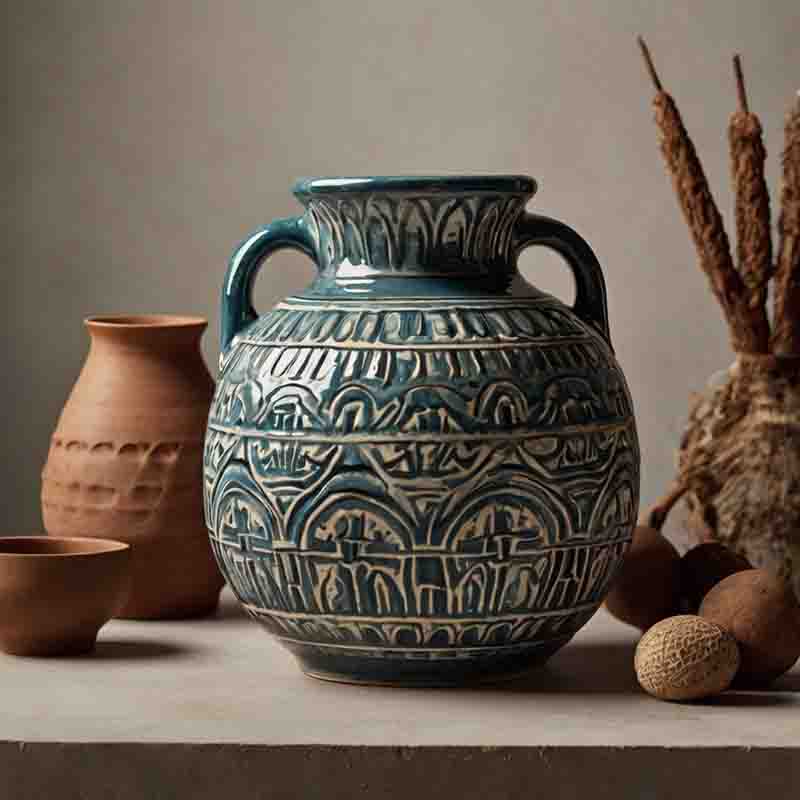
From simple pottery to advanced materials used in technology, ceramics have been part of human civilization for thousands of years.
Understanding Ceramic: An In-Depth Guide
Ceramics are an essential part of both our daily lives and human history, offering a wide range of uses across artistic, functional, and industrial domains.
From a simple coffee mug to advanced materials in the aerospace industry, ceramics cover an impressive spectrum of applications.
Understanding ceramics requires knowledge of their materials, techniques, firing processes, and applications.
What is Ceramic?
Ceramics are materials made from clay and other inorganic compounds that are shaped, hardened, and often glazed by applying heat.
This process gives ceramics their strength, durability, and unique ability to withstand extreme temperatures.
The word "ceramic" is derived from the Greek word "keramos," meaning "pottery" or "clay," and as such, ceramics include a vast range of products, from simple pottery to high-tech materials used in industrial applications.
The creation of ceramics begins with raw materials like clay, kaolin, silica, and feldspar, which are combined, shaped, and then fired in a kiln at high temperatures.
The high heat transforms these materials into hard, durable objects.
The versatility of ceramics is evident in the variety of items made, including functional goods such as dishes and pipes, as well as artistic creations like sculptures and tiles.
Ceramics are valued for their ability to retain their form and withstand heat, moisture, and chemicals, making them indispensable in industries ranging from construction to electronics and even medicine.
Types of Ceramic Materials
The main types of ceramics include porcelain, stoneware, earthenware, and advanced ceramics.
Each type varies in terms of firing temperature, texture, and strength.
Porcelain
Porcelain is considered the most refined form of ceramic.
Known for its strength and translucent appearance, porcelain is created by firing a special type of clay at very high temperatures, typically above 1,200°C.
The result is a smooth, white, and often delicate material.
Porcelain is widely used in fine china, decorative figurines, and high-end art pieces.
Stoneware
Stoneware is a more durable and denser ceramic, typically fired at slightly lower temperatures than porcelain.
This makes it less fragile, but still ideal for both decorative and functional uses.
Stoneware is commonly used for everyday items like dinnerware, mugs, and cookware.
It is also known for its natural, earthy textures and tones, retaining its clay color after firing.
Earthenware
Earthenware is the oldest and most commonly used ceramic material.
It is fired at a lower temperature than both porcelain and stoneware, making it more porous and less durable.
However, it is still widely used for decorative pottery and tiles.
Its charm lies in its rustic and simple appearance.
Earthenware is usually coated with a glaze to make it waterproof, which also enhances its aesthetic appeal.
Advanced Ceramic
Beyond traditional ceramics, advanced ceramics are used in cutting-edge applications such as electronics, aerospace, and medicine.
These materials include components like ceramic capacitors, heat shields, and even ceramic implants used in surgeries.
Advanced ceramics are made with more precise processes and are designed for specialized, high-performance applications.
Techniques in Ceramic Production
The production of ceramic items is a multi-step process that involves several techniques.
Each method offers distinct advantages depending on the desired outcome of the product.
Hand-Building
Hand-building is one of the oldest techniques in ceramic production, where artists manipulate the clay by hand rather than using a wheel.
The primary methods include coiling (building with long coils of clay), pinching (using fingers to shape the clay), and slab-building (cutting clay into flat sheets and assembling them).
These methods are ideal for creating unique, one-of-a-kind pieces.
The hand-building process allows for creativity and fine detail, which is why it remains popular for artistic pottery and sculptural works.
Wheel-Throwing
Wheel-throwing involves shaping the clay on a potter’s wheel.
This technique is perfect for making symmetrical and round forms such as bowls, vases, and cups.
The potter controls the clay by pressing and pulling it on the wheel as it spins, achieving a precise and uniform shape.
Wheel-throwing requires practice and skill to master, but it is an efficient way to create a wide range of functional pottery.
Slip-Casting
Slip-casting is a technique that involves pouring liquid clay (slip) into a mold.
This method is especially useful for creating highly detailed pieces and mass-producing identical items.
It is widely used in industries that require uniformity, such as the production of bathroom fixtures, dinnerware, and figurines.
The mold can be made of plaster, which absorbs water from the slip and allows the ceramic to harden into the mold’s shape.
Other Methods
In addition to the traditional methods mentioned above, modern technologies like 3D printing have been introduced into the ceramics field.
3D printing allows for precise, complex designs that were once difficult or impossible to achieve with manual techniques.
The rise of digital tools like CAD (Computer-Aided Design) has revolutionized the way ceramics are designed and produced, offering new possibilities for artists and manufacturers.
The Firing Process
Firing is a crucial step in ceramic production.
The firing process hardens the clay and can also apply a glaze, making the ceramic functional and durable.
Understanding Kilns
Kilns are specially designed ovens used to fire ceramics.
They come in different types, such as electric, gas, and wood-fired kilns, each offering different benefits.
Electric kilns are the most commonly used in modern studios, as they provide consistent and controllable heat.
Gas kilns are preferred by some artists for the unique effects they can achieve, such as those seen in reduction firing.
Wood-fired kilns, though rare in industrial production, are still used by traditional potters for their unique aesthetic outcomes.
Firing Stages
The firing process usually involves two stages.
The first is bisque firing, where the clay is heated to a point where it hardens but does not yet vitrify.
Bisque firing is necessary to remove any remaining moisture and organic materials in the clay.
After bisque firing, the ceramic is ready for glazing.
The second stage is glaze firing, where the glazed ceramic is fired again at a higher temperature to melt the glaze and fuse it to the surface.
The glaze creates a glossy or matte finish, depending on the type used, and provides a layer of protection to the ceramic.
Common Firing Issues
Firing ceramics is an intricate process that requires precision.
Common problems that can arise include cracking, warping, and glaze defects.
Cracking often occurs if the clay is not dried evenly before firing or if the firing temperature is too high too quickly.
Warping is another problem that can arise from uneven heat distribution.
Troubleshooting these issues requires careful control of the kiln’s temperature and the way ceramics are placed within the kiln.
Glazing and Surface Finishes
Glaze is a liquid coating applied to ceramics to give them a smooth, glossy finish.
It can also serve as a protective layer that makes the ceramic more durable.
What is Glaze?
Glazes are made from a mixture of water, minerals, and oxides.
When fired, the glaze melts and fuses to the surface of the ceramic, creating a glass-like appearance.
Different types of glazes produce varying finishes, from highly glossy to smooth matte surfaces.
Types of Glazes
There are several types of glazes, each providing a distinct aesthetic effect.
Glossy glazes give ceramics a shiny, reflective surface.
Matte glazes, on the other hand, provide a more subtle, non-reflective finish.
Transparent glazes allow the clay’s natural color to show through, while opaque glazes completely cover the surface.
Special effect glazes, such as celadon or crackle glazes, add unique textures and patterns to the surface.
Troubleshooting Glaze Problems
Sometimes glaze application doesn’t go as planned, leading to issues like pinholes, crawling, or blistering.
Pinholes can occur if there are air bubbles trapped in the glaze.
Crawling happens when the glaze pulls away from the ceramic, often due to uneven application.
Blistering is caused by trapped gases under the glaze that form bubbles.
By adjusting the glaze composition, applying thinner coats, and ensuring a proper firing schedule, many of these problems can be avoided.
Applications of Ceramic
Ceramics are not just decorative objects; they serve practical purposes in daily life and various industries.
Artistic Uses
Ceramics have long been a medium for artistic expression.
From ancient pottery to modern sculptures, ceramics offer artists a durable and malleable medium.
Decorative tiles, murals, and other artistic forms allow ceramics to shine in visual arts, combining both utility and aesthetics.
The fine art ceramic world is full of innovation, with artists constantly experimenting with textures, glazes, and forms.
Functional Applications
In daily life, ceramics are indispensable. Kitchenware, including mugs, bowls, plates, and cookware, is often made from ceramic.
These items are durable, heat-resistant, and provide aesthetic value to everyday tasks.
Tiles made from ceramic are also common, used in bathrooms, kitchens, and floors for their durability and ease of cleaning.
Industrial Applications
Ceramics are used extensively in industry for their heat resistance, strength, and insulating properties.
Ceramic materials are used in electrical insulators, automotive parts, and even in high-performance medical devices like dental implants and prosthetics.
In the aerospace industry, ceramic components like heat shields help spacecraft withstand the extreme heat of re-entry.
Cultural and Historical Importance
Ceramics have played a key role in human civilization, offering a rich window into history and culture.
Archaeological Insights
Ceramic artifacts provide valuable insights into the lives of ancient peoples.
Pottery found at archaeological digs reveals information about trade, daily life, and even social structures.
Different regions have developed their own unique ceramic traditions, such as Chinese porcelain, Greek pottery, and Native American clay vessels.
Evolution of Techniques
The evolution of ceramic production techniques mirrors advancements in human society.
From hand-building methods in ancient cultures to modern innovations in materials science, ceramics have adapted to meet the needs of their creators.
Maintenance and Conservation
Proper care and conservation techniques ensure ceramics remain functional and beautiful for years to come.
Caring for Ceramic
Ceramic items require proper cleaning and handling.
For daily use items like dinnerware, regular washing with non-abrasive cleaners is recommended to maintain the finish.
Decorative ceramics, such as sculptures or antique pieces, should be handled carefully to avoid chips or cracks.
Restoring Ceramic
If a ceramic item gets damaged, professional restoration can be an option.
Restoration techniques, such as using specialized adhesives or color matching glazes, can make even heavily damaged ceramics look as good as new.
Modern Innovations in Ceramic
Recent innovations in ceramic technology are pushing the boundaries of what is possible.
From 3D-printed ceramics to advanced bio-ceramics, the future of this material looks promising.
Ceramics are a fascinating and diverse material that impact our daily lives, industries, and art forms.
From their ancient origins to modern high-tech applications, ceramics have shown their adaptability and strength.
Understanding ceramics not only helps us appreciate their beauty and functionality but also their importance in the world today.
Ceramic refers to a category of materials that are made from inorganic, non-metallic compounds, typically derived from natural minerals such as clay, silica, and feldspar.
Ceramics are created by shaping these materials and then heating them at high temperatures to harden them.
The result is a durable, heat-resistant, and versatile material used in a variety of industries.
-
Ceramic Durability: The hardness of ceramics makes them resistant to scratching and damage, and their ability to withstand high temperatures makes them ideal for use in industries like aerospace and automotive manufacturing.
-
Ceramic Molding: Molds are typically made of plaster, and the liquid clay (slip) is poured into the mold to take the desired shape.
-
Ceramic Restoration: Techniques used in restoration include cleaning, filling cracks, and re-glazing.
-
Ceramic Manufacturing: Ceramic manufacturing involves the preparation of raw materials, shaping (such as molding or pressing), drying, firing in kilns, and sometimes glazing.
-
Ceramic Sculpture: Involves creating three-dimensional artworks from clay and other ceramic materials.
-
Ceramic Tiles: Commonly used for flooring, wall coverings, and bathroom surfaces due to their durability, ease of cleaning, and aesthetic versatility.
-
Ceramic Firing Process: The firing process can vary depending on the type of ceramic being produced and includes stages like bisque firing (pre-firing) and glaze firing (final firing).
-
Ceramic Industry: The ceramic industry encompasses businesses involved in the production, design, and distribution of ceramic products.
-
Ceramic Artwork: Ceramic art can range from functional pieces, like handcrafted mugs, to abstract and expressive sculptures that serve as visual representations of culture, emotion, or themes.
These expanded descriptions provide an in-depth understanding of each keyword related to ceramics, helping you grasp the wide range of applications and significance of ceramics in both artistic and industrial contexts.
Significance of Ceramic
Ceramic refers to objects made from clay and other inorganic materials, shaped and hardened through high heat.
Common types include porcelain, stoneware, and earthenware.
Ceramics are used in art, industry, and daily life, offering durability, heat resistance, and versatility.
Techniques like hand-building, wheel-throwing, and slip-casting shape ceramics for decorative and functional purposes.
Ceramic: FAQ
Are you curious about music, art, technology, fashion, lifestyle, and beer?
If so, then you need to subscribe to the free Likewolf newsletter.
100% privacy. When you sign up, we'll keep you posted.
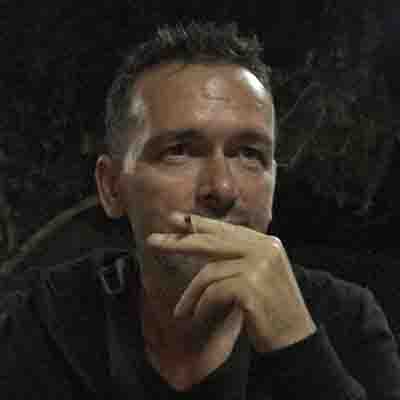
Likewolf's Typewriter
Likewolf writes about music, art, technology, fashion, lifestyle, and beer
LikewolfThe Silent Language of Clay
From Prehistoric Pottery to Modern Art